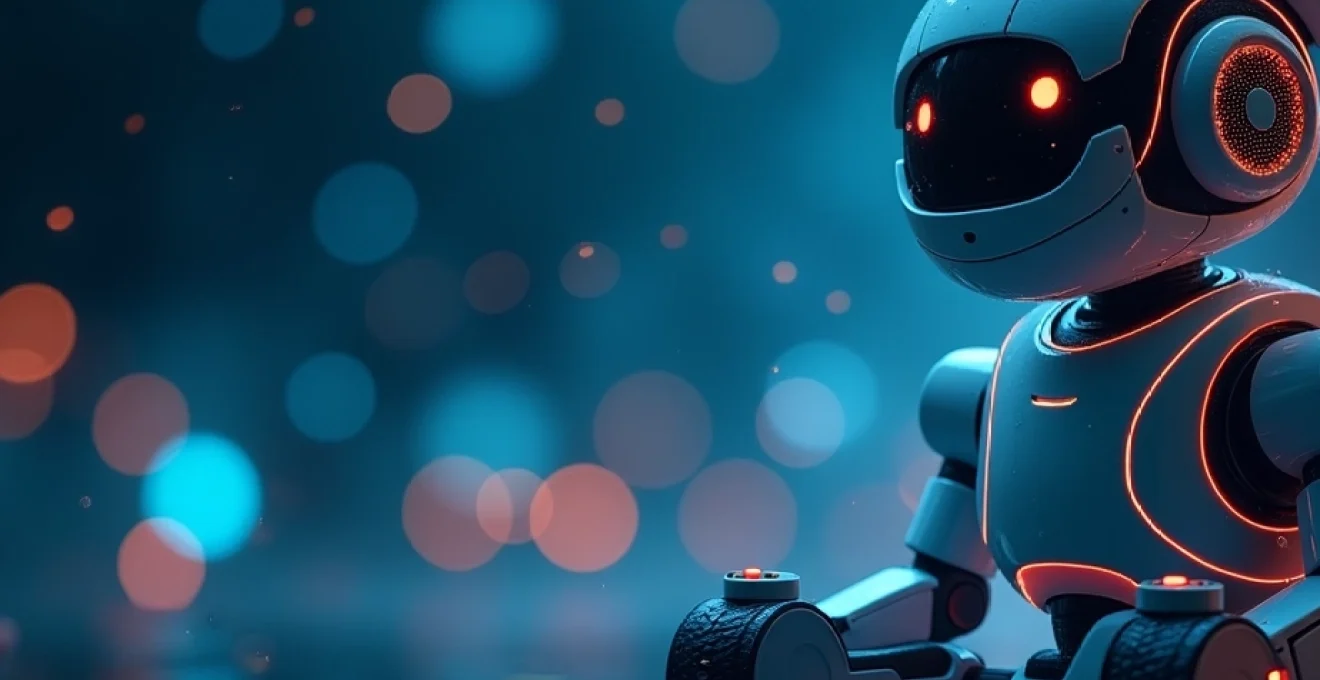
The robotics industry is undergoing a transformation, driven by advancements in sensor technology. Intelligent sensors are revolutionizing how robots perceive and interact with their environment, enabling unprecedented levels of autonomy and adaptability. As the demand for more sophisticated robotic systems grows across industries, from manufacturing to healthcare, the integration of next-generation sensors is becoming crucial for enhancing performance, safety, and efficiency.
These cutting-edge sensors are not only improving the capabilities of individual robots but are also paving the way for more complex and coordinated robotic systems. By providing robots with enhanced perception and decision-making abilities, intelligent sensors are expanding the scope of tasks that can be automated, opening up new possibilities for innovation and productivity gains in various sectors.
Advanced sensors enabling smarter robotic automation
The evolution of robotic systems is intrinsically linked to advancements in sensor technology. Today's robots are equipped with a diverse array of sophisticated sensors that allow them to gather and process vast amounts of data about their surroundings. This enhanced sensory capability is the foundation for more intelligent and responsive robotic behavior.
One of the key advantages of advanced sensors is their ability to provide robots with real-time, high-resolution data about their environment. This enables robots to make more informed decisions and adapt quickly to changing conditions. For instance, in manufacturing environments, robots equipped with advanced vision sensors can detect minute defects in products that would be invisible to the human eye, ensuring higher quality control standards.
Moreover, the integration of multiple sensor types allows robots to build a more comprehensive understanding of their environment. By combining data from various sensors, robots can create detailed 3D maps of their surroundings, identify and track objects with greater accuracy, and navigate complex spaces with increased precision.
Advanced sensors are the eyes and ears of modern robotics, enabling machines to perceive and understand their environment in ways that were previously impossible.
The impact of these sensors extends beyond simply improving existing capabilities. They are enabling entirely new applications for robotics, such as autonomous vehicles that can safely navigate busy streets, surgical robots that can perform delicate procedures with superhuman precision, and collaborative robots that can work alongside humans in dynamic environments.
Intelligent sensors powering next-generation robotics
The latest generation of intelligent sensors is characterized by their ability to not only collect data but also to process and analyze it on the spot. This edge computing capability allows for faster response times and reduced reliance on central processing units, making robots more autonomous and efficient.
These intelligent sensors are often equipped with machine learning algorithms that enable them to improve their performance over time. As they gather more data and experience different scenarios, they can refine their ability to interpret sensory inputs and make more accurate predictions about future events or outcomes.
Vision sensors for enhanced robot perception
Vision sensors have undergone significant advancements in recent years, with the development of high-resolution cameras, 3D depth sensors, and sophisticated image processing algorithms. These improvements have dramatically enhanced robots' ability to perceive and interpret visual information.
Modern vision sensors can capture and process images at high frame rates, allowing robots to track fast-moving objects with precision. They can also operate in challenging lighting conditions and distinguish between subtle variations in color and texture. This level of visual acuity is crucial for tasks such as quality inspection, object recognition, and autonomous navigation.
For example, in warehouse automation, robots equipped with advanced vision sensors can quickly identify and sort different types of packages, regardless of their orientation or position. This capability significantly improves the efficiency and accuracy of logistics operations.
Force sensors improving robot tactile capabilities
Force sensors are giving robots a sense of touch, allowing them to interact with objects and surfaces with greater finesse. These sensors can measure the amount of force applied in multiple directions, enabling robots to handle delicate items without damaging them or to apply precise amounts of pressure for tasks like assembly or machining.
The latest force sensors are highly sensitive and can detect even slight variations in pressure. This sensitivity allows robots to perform tasks that require a delicate touch, such as handling fragile electronic components or assisting in medical procedures.
In the field of robotic surgery, force sensors play a crucial role in providing surgeons with haptic feedback, allowing them to "feel" the tissue they are operating on through the robotic interface. This tactile information enhances the surgeon's control and precision, leading to better patient outcomes.
Environment sensors enabling adaptive robot behavior
Environment sensors encompass a wide range of devices that measure various aspects of the surrounding conditions, including temperature, humidity, air quality, and even chemical composition. These sensors allow robots to adapt their behavior based on environmental factors, ensuring optimal performance and safety.
For instance, in agricultural robotics, sensors that measure soil moisture, nutrient levels, and plant health can guide autonomous farming robots to apply water and fertilizers precisely where they are needed. This targeted approach not only improves crop yields but also conserves resources and reduces environmental impact.
In industrial settings, environment sensors can detect the presence of hazardous gases or extreme temperatures, alerting human operators and triggering appropriate safety protocols. This capability is particularly valuable in scenarios where robots are deployed in dangerous or inhospitable environments.
Sensor fusion techniques optimizing robot performance
Sensor fusion is a critical technique in modern robotics that combines data from multiple sensors to create a more accurate and comprehensive understanding of the environment. By integrating information from various sources, robots can overcome the limitations of individual sensors and make more reliable decisions.
The process of sensor fusion involves sophisticated algorithms that analyze and correlate data from different sensors in real-time. This integration allows robots to compensate for the weaknesses of one sensor type with the strengths of another, resulting in more robust and reliable performance across a wide range of conditions.
Multi-modal sensor integration for improved accuracy
Multi-modal sensor integration involves combining data from different types of sensors, such as visual, auditory, and tactile inputs. This approach mimics the way humans use multiple senses to understand their environment, leading to more natural and intuitive robot behavior.
For example, a robot equipped with both vision and force sensors can not only see an object but also feel its weight and texture when grasping it. This combined sensory information allows the robot to handle objects more skillfully, adapting its grip and movement based on the object's properties.
In autonomous vehicles, multi-modal sensor integration is crucial for safe navigation. By fusing data from cameras, LiDAR, radar, and ultrasonic sensors, these vehicles can create a comprehensive 360-degree view of their surroundings, detecting obstacles and predicting potential hazards with greater accuracy than any single sensor could provide.
Sensor data fusion algorithms boosting efficiency
Advanced sensor data fusion algorithms are the brains behind the integration of multiple sensor inputs. These algorithms use techniques such as Kalman filtering, particle filtering, and machine learning to process and combine data streams efficiently.
One of the key benefits of sensor data fusion is the ability to reduce noise and uncertainty in sensor readings. By comparing and correlating data from multiple sources, these algorithms can filter out erroneous readings and produce more reliable results. This improved accuracy translates into smoother robot movements, more precise object manipulation, and better overall performance.
Furthermore, sensor data fusion can help optimize the use of computational resources. By intelligently combining and processing sensor data, robots can extract relevant information more efficiently, reducing the need for excessive data transmission and processing.
Adaptive sensor fusion for dynamic environments
The latest sensor fusion techniques are not static but adaptive, capable of adjusting their parameters and strategies based on the current situation. This flexibility is crucial for robots operating in dynamic environments where conditions can change rapidly.
Adaptive sensor fusion allows robots to prioritize certain types of sensor data depending on the task at hand or the environmental conditions. For instance, in low-light conditions, a robot might rely more heavily on infrared or ultrasonic sensors rather than visual cameras. Similarly, when performing a precision assembly task, force sensors might take precedence over other inputs.
This adaptability extends to the ability to reconfigure sensor networks on the fly, activating or deactivating sensors as needed to conserve energy or focus on specific aspects of the environment. Such dynamic reconfiguration ensures that robots can maintain optimal performance across a wide range of scenarios.
Intelligent sensor networks coordinating robot fleets
As robotics applications scale up, there is an increasing need for coordination among multiple robots working together. Intelligent sensor networks are playing a crucial role in enabling effective communication and collaboration within robot fleets.
These networks consist of interconnected sensors distributed across multiple robots and the environment. They create a shared pool of sensory data that can be accessed and utilized by all members of the robot fleet, enhancing collective intelligence and coordination.
One of the key advantages of intelligent sensor networks is their ability to provide a more comprehensive view of the operating environment. By combining data from sensors on multiple robots, these networks can create detailed maps of large areas, track moving objects across wide spaces, and identify patterns or anomalies that might not be apparent to individual robots.
Moreover, intelligent sensor networks enable more efficient resource allocation within robot fleets. By sharing real-time information about their status and the tasks they are performing, robots can dynamically redistribute workloads, avoiding duplication of effort and ensuring that the most suitable robot is assigned to each task.
Intelligent sensor networks are the nervous system of coordinated robot fleets, enabling seamless communication and collaboration for enhanced productivity.
These networks also play a crucial role in ensuring safety and collision avoidance in multi-robot environments. By constantly monitoring the positions and trajectories of all robots in the fleet, the network can predict and prevent potential conflicts, allowing robots to navigate shared spaces safely and efficiently.
Miniaturized smart sensors expanding robot applications
The trend towards miniaturization in sensor technology is opening up new possibilities for robotics applications. Smaller, more powerful sensors are enabling the development of compact robots that can operate in previously inaccessible environments and perform tasks at microscopic scales.
These miniaturized smart sensors often integrate multiple sensing modalities into a single, compact package. For example, a single chip might contain accelerometers, gyroscopes, magnetometers, and pressure sensors, providing a wealth of data about the robot's motion and orientation in a tiny form factor.
Micro sensors enabling small-scale robotic tasks
Micro sensors are pushing the boundaries of what's possible in robotics, particularly in fields like medical technology and microelectronics manufacturing. These sensors, often no larger than a few millimeters, can detect and measure phenomena at the microscopic level with incredible precision.
In the medical field, micro sensors are enabling the development of miniature robotic devices that can be inserted into the human body for diagnostic or therapeutic purposes. These microrobots can navigate through blood vessels, take measurements, deliver targeted treatments, and even perform minimally invasive surgeries.
In manufacturing, micro sensors allow robots to manipulate and assemble components at the microscale. This capability is particularly valuable in the production of microelectronics, where precise positioning and manipulation of tiny components is crucial.
Embedded sensors for autonomous mobile robots
Embedded sensors are integral to the development of autonomous mobile robots, providing these machines with the ability to navigate and interact with their environment independently. These sensors are typically built directly into the robot's structure, offering a seamless and robust sensing solution.
Modern autonomous mobile robots often incorporate a suite of embedded sensors, including:
- Inertial measurement units (IMUs) for tracking motion and orientation
- Proximity sensors for obstacle detection and avoidance
- Environmental sensors for monitoring temperature, humidity, and air quality
- GPS receivers for outdoor navigation
The integration of these sensors allows mobile robots to build accurate maps of their surroundings, localize themselves within those maps, and plan efficient paths to their destinations. This capability is crucial for applications such as warehouse automation, where robots need to navigate complex and dynamic environments safely and efficiently.
Wearable sensors enhancing human-robot collaboration
Wearable sensors are bridging the gap between humans and robots, enabling more intuitive and natural interactions. These sensors can be integrated into clothing, gloves, or other wearable accessories, allowing humans to control robots through gestures or monitor their own physiological state during collaborative tasks.
In industrial settings, wearable sensors can enhance safety by monitoring workers' vital signs and alerting them to potential hazards. They can also track workers' movements and posture, providing feedback to improve ergonomics and reduce the risk of injury.
For human-robot collaboration, wearable sensors enable more precise and responsive control of robotic systems. For instance, a worker wearing sensor-equipped gloves can guide a robot's movements with natural hand gestures, making it easier to perform complex tasks that require human judgment and robot precision.
As wearable sensor technology continues to advance, it is likely to play an increasingly important role in creating more seamless and productive human-robot interactions across various industries.
The integration of next-generation intelligent sensors is revolutionizing the field of robotics, enabling machines to perceive, understand, and interact with their environment in increasingly sophisticated ways. From enhancing the capabilities of individual robots to enabling coordinated fleets and facilitating human-robot collaboration, these sensors are driving innovation and expanding the potential applications of robotic technology.
As sensor technology continues to evolve, we can expect to see even more advanced and capable robotic systems emerging, transforming industries and opening up new possibilities for automation and human augmentation. The future of robotics is intrinsically linked to the development of smarter, more versatile sensors, promising a world where intelligent machines play an ever-more significant role in our daily lives and work.